The HLB Concept
- jessicawieland
- Feb 8, 2019
- 3 min read
Updated: Aug 24, 2023
Introduction to the use of HLB in surfactant selection for emulsification.
In developing emulsifier systems, it is important to select a surfactant/emulsifier system with the correct characteristics to match the requirements of the oil phase plus other factors, such as the temperature of the emulsion and electrolytes.
The use of the HLB system can help in quickly identifying the optimum surfactant system.
HLB = Hydrophile - Lipophile Balance
It provides the starting point for matching the HLB of the surfactant with the required HLB of the oil to form stable emulsions. One can predict the approximate HLB needed to emulsify a given material and make more intelligent estimates of which surfactant or combinations of surfactants are appropriate to a given application. When blends are used the HLB can be
estimated by using a weighted average of the surfactants used in the blend.

Calculation of the HLB of nonionic surfactants
This method has proved very successful with alkoxylated nonionic surfactants but
less successful with ionic surfactants. The HLB system, in it's most basic form, allows for the calculation of HLB using the following formulation :
HLB = % Hydrophile by weight of molecule
5
Example: Oleyl alcohol 10 EO
Molecular weight of hydrophile we calculate the molecular weight of the 10 moles of ethylene oxide (one mole EO =44)
10 x 44 = 440
We add this number to the molecular weight of the oleyl alcohol
440+ 270 = 710
What percentage of 710 is 440?
440 / 710 *100= 61.97%
Therefore: HLB is 61.97/5 = 12.4
Example of HLB mixture calculation
HLB of a blend of two surfactants, 70 wt% Lansurf SMO80 (HLB=15) and 30 wt% Lansurf SMO (HLB=4.3) can be computed as follows:
HLB mixture = 0.3 x 4.3 + 0.7 x 15 = 11.8
Similarly for a 70:30wt% mixture of oleic acid (HLB=17) and lanolin (HLB=12):
HLB mixture = 0.7 x 17 + 0.3 x 12 = 15.5
The HLB values measured against solubility in water
The HLB of a surfactant, ranging from 1 to 20, affects its characteristics in aqueous solutions and dictates their characteristics and the typical applications where they will be used.
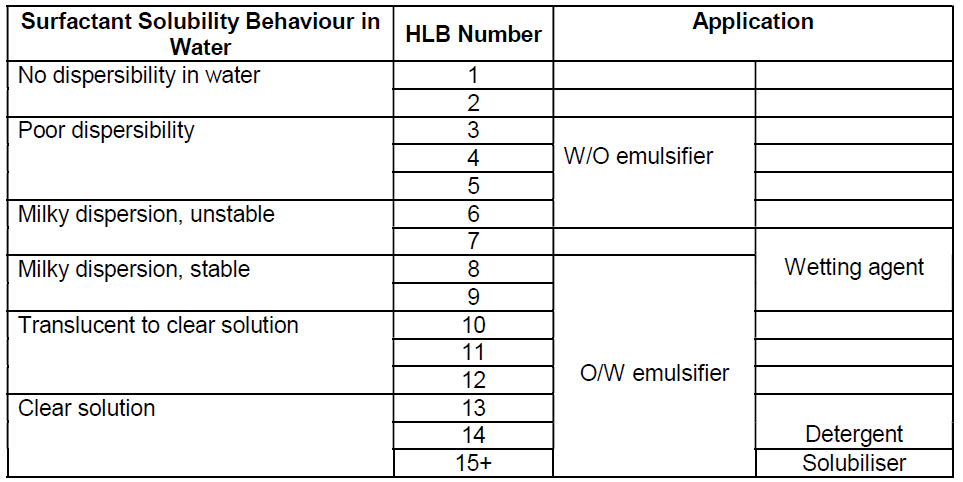
An emulsion is most accurately defined as a dispersion of liquid droplets in a second immiscible liquid. Temporary emulsions may be formed by mixing the two normally immiscible liquids, however, the stability of temporary emulsions produced in this way is poor. Emulsifiers are surface-active materials (surfactants) that are used to assist in the formation and stabilisation of an emulsion.
The optimum emulsifier will also be dictated by the external phase, with oil in water emulsion requiring higher HLB emulsifier systems than water in oil.

When determining the optimum HLB the nature of the oil phase and the emulsion type (oil in water or water in oil) is the starting point. There are literature values available for several materials:

Example Emulsification of paraffinic mineral oil
The literature HLB value for the emulsification of paraffinic mineral oil is 10, but this is an approximate value as the exact HLB will be effected by the composition of the specific oil, plus the HLB values assigned to emulsifiers are not particularly accurate, therefore the optimum HLB for each oil and emulsifier needs to be established by experimentation.
This is achieved by preparing emulsions based on blends of emulsifiers to give HLB’s around the theory value as in the table below. Based on the emulsion quality the optimum ratio and HLB can be determined. It may be necessary to make further blends, for example if the best result is obtained with sample 6 further blends with HLB’s of 9.3 and 9.1 should be evaluated.

Using blends of surfactants has a number of benefits. Firstly it allows the optimum HLB to be used for each application. Also in many applications, blending emulsifiers with different HLB’s can be beneficial, to provide a broader range of HLB’s present in the system. This is often beneficial when the oil phase is a mixture rather than an individual chemical species. Blending nonionic and anionic emulsifiers can also be beneficial, in many applications it can increase the stability in applications where a wide range of temperatures can occur.

Sometimes the HLB of the oil may not be known. In this case experimental analysis using a range of nonionic surfactants with varying degrees of ethoxylation but with the same hydrophobe is a good starting method to establish an approximation of the emulsifiers HLB.
Lankem manufactures a wide range of emulsifiers, the following table provides information on their HLB values:
Product | Description | HLB |
Sorbitan tri-oleate | 1.8 | |
Sorbitan mono-oleate | 4.3 | |
Sorbitan mono-stearate | 4.7 | |
Cetyl oleyl + 3EO | 6.8 | |
Castor oil + 12EO | 7.0 | |
C10 alcohol + 3EO | 8.0 | |
Sorbitan mono-laurate | 8.0 | |
C13 alcohol + 3EO | 9.0 | |
C10 alcohol + 5EO | 10.0 | |
Sorbitan mono-oleate + 5EO | 10.0 | |
Oleic acid + 7EO | 10.4 | |
C13 alcohol + 5EO | 10.5 | |
Sorbitan tri-oleate + 20EO | 11.0 | |
Oleic acid + 10EO | 11.8 | |
C10 alcohol + 7EO | 12.0 | |
C13 alcohol + 7EO | 12.0 | |
BioLoop 68L | 100% Biobased BioLoop | 12.5 |
C13 alcohol + 10EO | 13.5 | |
Castor oil + 40EO | 13.5 | |
Oleic acid + 14EO | 13.6 | |
C10 alcohol + 9EO | 14.0 | |
BioLoop 84L | 100% Biobased BioLoop | 14.2 |
Tallow amine + 15EO | 14.2 | |
C10 alcohol + 8EO | 14.5 | |
C13 alcohol + 12EO | 14.5 | |
Sorbitan mono-oleate + 20EO | 15.0 | |
Sorbitan mono-stearate + 20EO | 15.0 | |
C13 alcohol + 15EO | 15.5 | |
C13 alcohol + 20EO | 16.5 | |
Sorbitan mono-laurate + 20EO | 16.5 | |
Tallow amine + 30EO | 16.6 | |
Cetyl oleyl + 35EO | 17.0 |
Further reading: The Principles of emulsification
Commenti