High Gloss Non-Aqueous Titanium Dioxide Coatings
- Dr Cathy Cooper
- Mar 19
- 4 min read
Introduction
Titanium dioxide is the largest volume pigment used in the paint, coatings and inks market. When used for coating applications, it is predominantly present as the rutile-type crystal structure. To reduce the photoactivity of the pigment, the rutile TiO2 crystal is modified with other metal oxides. In addition, very thin films of inorganic oxides (such as alumina, silica, or zirconia) are deposited onto the pigment surface to influence the adsorption of additives.
The primary particle size of TiO2 for "hiding"-type applications is usually 0.25-0.3 µm. Organic surface treatments (trimethylolpropane, neopentyl glycol, various surfactants, silicones) are often utilized to improve the dispersibility of TiO2 in organic or aqueous media. These organic treatments alone, in most cases, do not provide sufficient stabilization for proper deflocculation of the pigment and, therefore, paint producers must use additional additives in order to achieve the maximum level of pigment stabilization. This blog will look at initial laboratory work undertaken by Lankem Ltd. in non-aqueous systems, comparing our newly developed high molecular weight dispersants with market standards.
The two non-aqueous systems covered here are one solvent-based dispersion of Tioxide TR92 in PMA (propylene glycol methyl ether acetate) alongside a common aldehyde resin, and a UV dispersion of Sachtleben RDI-S with DPGDA (dipropylene glycol diacrylate) as the medium.
Solvent-Based System Formulation and Results
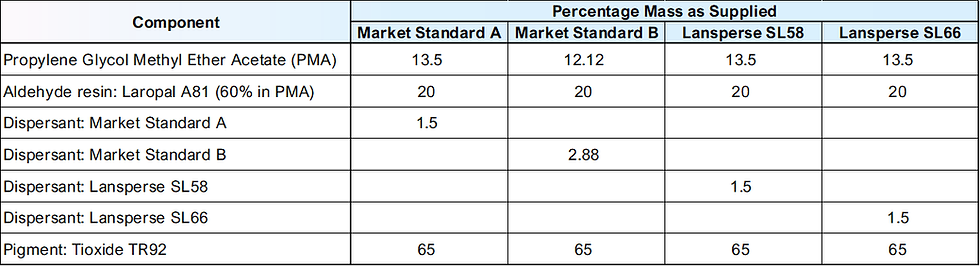
Pre-mixes were made using a high speed mixer, adding ingredients as specified in Table 1 with the dispersant and PMA mixed first before addition of pigment. The titanium dioxide slurry was allowed to stir for 5 minutes before the dispersion was transferred to a Silverson and homogenised for 15 minutes at 4000 rpm, to a Hegmann gauge level of less than 7. Solvent-based dispersions were coated onto LENETA card at a wet film thickness of 12 µm, using a TQC automatic k-bar applicator. These were left to dry at room temperature, and gloss was measured at 20 °. The viscosity of the dispersion was also measured using a DIN flow cup, initially and following storage at room temperature.


It can be seen from the graphs and table above that Lansperse SL58 and Lansperse SL66 allow for a significantly higher gloss at an incidence angle of 20° than the two market standard dispersants tested. The viscosity of the dispersion was evaluated using the DIN flow cup method over a number of days storage at room temperature, and the Lansperse products gave comparable performance to the market standards in these measurements. Lansperse SL58 provided the most optimal balance of low dispersion viscosity with an improvement in coating gloss in this particular testing system.
UV System Formulation and Results
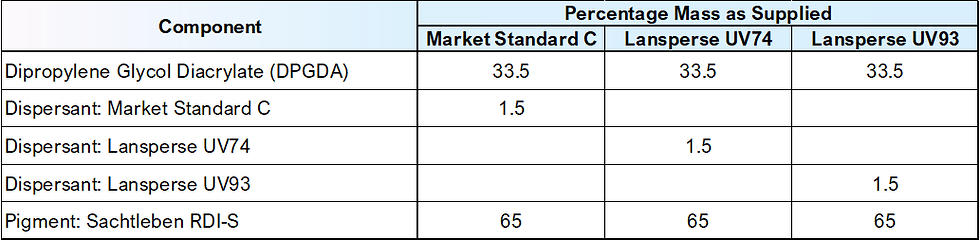
Pre-mixes were made using a high speed mixer, adding ingredients as specified in Table 3 with the dispersant solubilised in the DPGDA first before addition of pigment. The titanium dioxide slurry was allowed to stir for 5 minutes before the dispersion was transferred to a Silverson and homogenised for 15 minutes at 4000 rpm, to a Hegmann gauge level of less than 7. To obtain suitable inks, the titanium dioxide dispersion was let-down into the formulation outlined in Table 4 to give a final pigment loading of 26 % w/w. The ink formulations were coated onto LENETA card at a wet film thickness of 12 µm, using a TQC automatic k-bar applicator, and cured using a GEW laboratory UV unit.
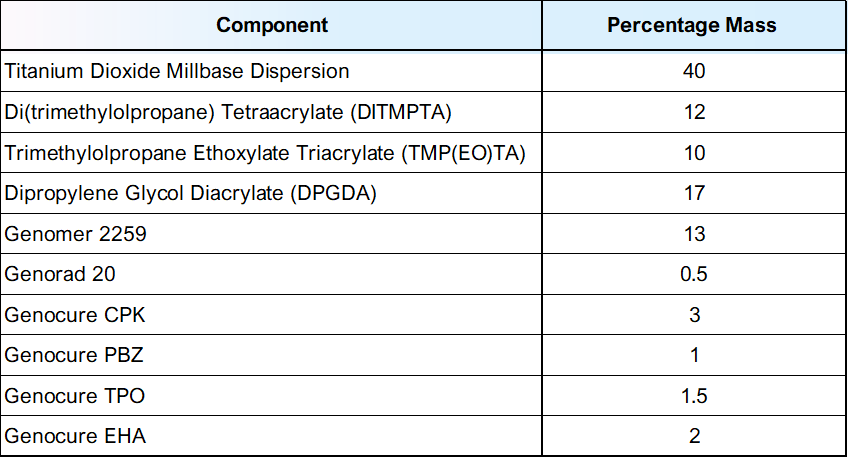
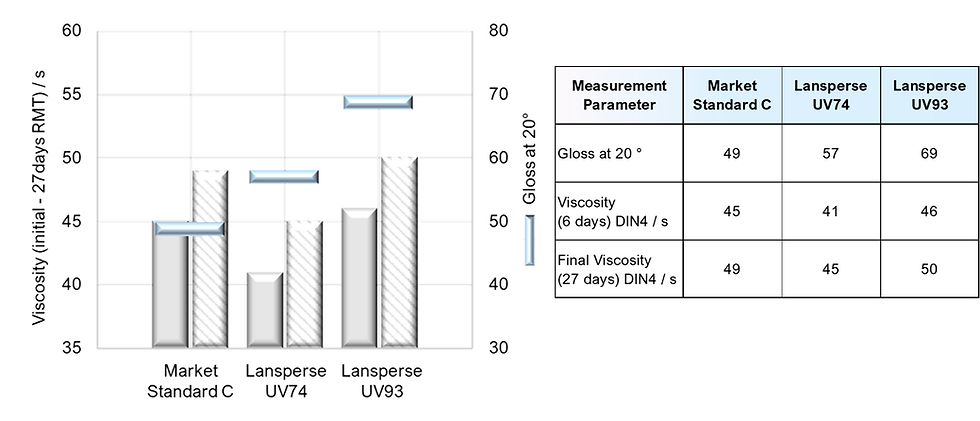
The Lankem Ltd. dispersants tested here, Lansperse UV74 and Lansperse UV93, both gave excellent dispersion performance, with Lansperse UV74 offering a slight advantage in lower millbase viscosity. The gloss at 20° was high for the final inks, and Lansperse UV93 provided a particularly good mix of comparable dispersion viscosity to Market Standard C, with significantly higher gloss.
Conclusion
In this screening study of solvent and UV white formulations, the new high molecular weight dispersants from Lankem Ltd. offer the potential for high gloss systems. The improvement in gloss also appears in solvent-based black systems, and more details can be found in the blog post Solvent-Based Carbon Black Dispersions.
Product Links
All information, recommendations and suggestions appearing in the literature concerning the use of the products are based upon tests and data believed to be reliable. However it is the users responsibility to determine the suitability for their own use of the products described here, and we recommend testing a range of dispersant loading levels.
Comments